Type B TDA
Typical size:
12 inch minus
Volume measures:
1 ton = 1.5 cubic yards
1 ton = 100 tires
In place density: 45-50 lbs. per cubic foot
Permeability: >1cm/sec for many applications
Uses:
Lightweight and conventional fill for embankments
Lightweight backfill for retaining walls
Vibration mitigation
Tire Derived Aggregate (TDA) – Overview
Tire derived aggregate (TDA) consists of scrap tires cut into pieces that have a basic geometrical shape and range between 2 inches (50 mm) and 12 inches (305 mm) in size and are intended for use in civil engineering applications” (ASTM D6270-08).
There are two types of TDA: Type A with a maximum size of 3 in. (75 mm) and Type B with a maximum size of 12 in. (305 mm). While these are the most commonly used sizes, TDA specifications are determined by the end use and will differ based on the contractor’s technical, environmental and economic requirements for the project. TDA has become the commonly accepted description for this material because it better conveys the intrinsic engineering value of size-reduced scrap tire pieces as compared to the term tire chip or tire shred. However, the terms are often used interchangeably.
BENEFITS of TDA
- Lightweight (weighs 1/3 of what soil weighs)
- Low earth pressure (1/2 that of soil)
- Good thermal insulation (8 times better than gravel)
- Good drainage (10 times better)
- Compressible
- Vibration mitigation
- Low cost
USES INCLUDE
- Construction of retaining walls
- Drainage culverts
- Road-base reinforcement
- Erosion protection
- Fill material – whole baled tires
PHYSICAL PROPERTIES
- Gradation
- Specific gravity/water absorption
- Unit weight
- Thermal conductivity
- Compressibility
- Resilient modulus
- Sheer strength
- Ateral earth pressure
- Time dependent settlement
- Permeability
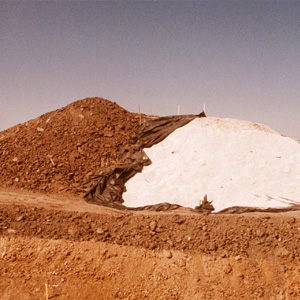
Drainage or Backfill
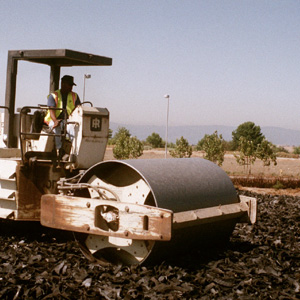
Gravel Alternative
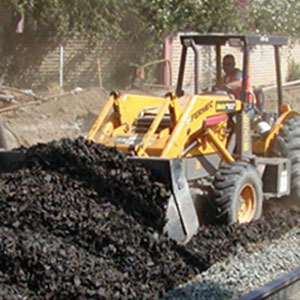
Civil Engineering Projects
Unit Costs
For PRICE QUOTES
Give us a call at
(970) 878-4444
Or fill out the contact form below
TDA Processing
In general, tire derived aggregate can be made from passenger and truck tires or a mixture of tire sizes. The tire feedstock for TDA can be derived from current flow tires, stockpiled tires or site cleanup tires.
To prepare TDA, tires are fed into a primary shredder that cuts the tires using knives that rotate at slow speed. The most popular type of primary shredder consists of groups of spaced circular blades mounted on pairs of counter-rotating shafts. Opposite each blade on one shaft, a spacer of equal width on the other shaft permits the blades to counter-rotate in overlapping fashion. Ideally, the knife blades operate with small clearances in the overlap area. This type of primary shredder has hooks on the knives that help pull the tire into the blades and cut the tire lengthwise. The corners of the knives act as cutting edges that together with the adjoining blade edges of the knives on the opposing shaft create the scissor action needed to cut the tires.
Another type of primary shredder utilizes knife rotors and rotor spacers that are permanently attached to the knife rotors. The machine has detachable blade sections bolted to the knife rotor. Wear plates or liners are also secured to each side of the rotor to protect against wear. This machine design permits closer spacing tolerance between the edges of the adjacent blade than can be achieved with conventional hook and shear machines. Feed rollers align and feed tires to the knives in this type shredder. In general, for both type shredders the width of a tire shred is controlled by the knife spacing while the length of a shred can be as much as the diameter of the tire. A single pass through the primary shredder’s knife configuration usually produces hoop-shaped strips of tire sections of varying lengths and the width of the blade cutters.
Have Questions?
If you have any questions about our Tire Shreds–
give us a call at (970) 878-4444